Motori
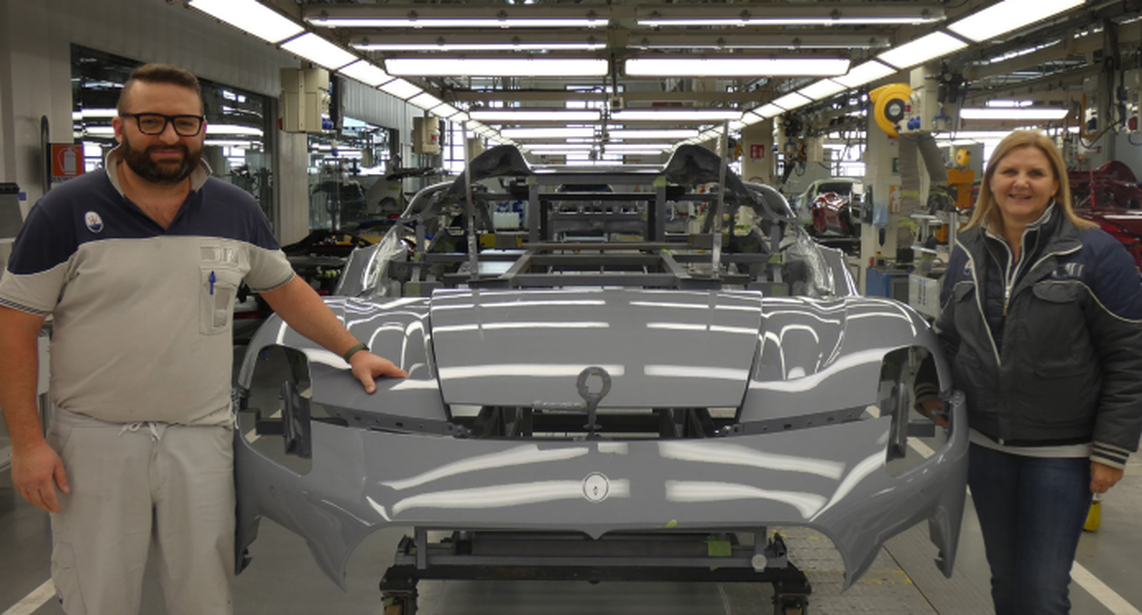
Indaffarati nelle loro tute grigie e blu, gli artigiani della velocità Maserati si muovono con sicurezza e familiarità tra i pistoni, i cavi e le ruote del padiglione dedicato al montaggio delle auto grazie a dei particolari carrelli. A catturare immediatamente l’attenzione, appena entrati nell’area produttiva tridentata, ci sono piccoli gruppi di operai suddivisi in stazioni parallele, che attendono pazientemente questa sorta di piattaforme fluttuanti. Le Agv (Automated guided vehicle), i carrelli rettangolari e silenziosi, forniti di luci colorate, sono infatti l’elemento essenziale che dà inizio al processo di montaggio delle auto. A dominare la scena di lavoro e le strade che connettono il polo produttivo di Ciro Menotti, c’è il simbolo del Nettuno, marchio identificativo Maserati dai tempi della sua fondazione. Il torrione col tridente rosso, visibile già quando il treno si avvicina a Modena, è un esplicito riferimento alla statua del Giambologna che troneggia nell’omonima piazza di Bologna. Oggi, all’interno dei padiglioni in cui la scuderia si trasferì nel 1939 – dopo essere stata ceduta due anni prima dai fratelli Maserati all’imprenditore modenese Adolfo Orsi (attualmente la proprietà è di Stellantis) – lavorano cento dipendenti suddivisi in due filoni produttivi.
Quaranta operai si occupano della verniciatura e preparazione della carrozzeria, altri sessanta sono coinvolti nelle fasi del montaggio. Da più di ottant’anni, il tridente modenese richiama appassionati del lusso e della velocità in questo micromondo tecnologico a quattro ruote. Ma come si combinano le varie parti per far nascere i bolidi che rendono la città della Ghirlandina una tappa essenziale del turismo automobilistico? La scocca è lo scheletro dell’auto a cui man mano vanno aggiunte vene e arterie (i fili e cavi), muscoli e organi (interni, sedili e cruscotto) e la pelle (la carrozzeria). A trasportare la scocca dell’auto tra le varie stazioni del montaggio sono appunto i carrelli rettangolari (Agv). «La scocca in carbonio arriva direttamente dal fornitore. In una prima fase si uniscono il telaio anteriore a quello posteriore e poi, nella stazione successiva, montiamo sul modello spider l’anello parabrezza e sul coupé il tetto» spiega Michela Lomio, responsabile produttiva dell’impianto. Come chirurghi, gli operai sprofondano tra le parti di acciaio per inserire e collegare i cavi dei sistemi elettronici e meccanici e montare il cruscotto. A questo punto avviene uno dei passaggi più importanti e affascinanti del processo. L’auto in costruzione abbandona solo per questa fase il suo tappeto magico e automatico per essere sospesa a mezz’aria tramite un gancio, una posizione non dissimile da quei peluche che si tenta di vincere nelle macchinette che spesso si trovano nei centri commerciali.
«In ogni fase del processo abbiamo pensato di posizionare l’auto in modo da agevolare le postazioni di lavoro dei dipendenti, che durante le fasi di montaggio devono essere comodi: i ganci che sollevano l’auto e il carrello che la trasporta rispondono all’esigenza di mantenere delle posizioni ergonomiche» prosegue Lomio. Il passaggio ha riacquisito un sapore tutto nuovo: difatti il polo modenese si sta occupando della costruzione della nuova supercar Mc20 cielo le cui componenti sono tornate ad essere interamente made in Maserati (dopo la parentesi motori e vernici Ferrari).
Attualmente vengono prodotte, in media, sei Mc20 Cielo (modello spider) e una Mc20 coupé al giorno, mentre del modello Mc20 Notte è stata inaugurata una serie esclusiva di cinquanta esemplari. Questa scelta sembra aver avvantaggiato la scuderia modenese nel 2022, anno in cui ha raggiunto un fatturato di 2,3 miliardi, in aumento del 14,7% rispetto all’anno precedente. Il volume positivo delle vendite Maserati sembra però aver cambiato tendenza, registrando una forte battuta d’arresto dal terzo trimestre dello scorso anno. Il drastico calo degli ordini, dovuto soprattutto alla diminuzione della richiesta dal mercato cinese, ha determinato l’attivazione di tre settimane di cassa integrazione per 220 lavoratori dell’intera azienda modenese tra la fine di gennaio e l’inizio di febbraio.
Intanto, sul comparto motori e alimentazione, l’azienda sta puntando sull’elettrificazione. L’ad Davide Grasso ha infatti dichiarato: «Entro il 2025 ogni auto avrà il suo modello corrispondente in elettrico ed entro il 2030 produrremo tutto in elettrico». Per completare il proprio tragitto il gancio che sospende l’auto a mezz’aria successivamente si abbassa, posizionando la vettura nuovamente sul carrello. Dopo le sospensioni, il bolide comincia ad assumere un aspetto più familiare mentre gli operai fissano gli interni e le ruote. «Dopo la fase del montaggio interni e del montaggio ruote, il carrello va via, pronto a iniziare un nuovo processo» ci indica Lomio mentre questo prezioso aiutante si allontana. In questa fase, Francesco Di Palo, team leader alla Maserati da 21 anni, racconta che «ci si occupa dei giochi e dei profili della vettura, delle luci e della compattezza della macchina, perché il suo profilo deve essere uniforme e perfetto». Simone Brescia, operaio in trasferta da un anno nella sede tridentata, racconta che c’è «una tabella in millimetri da rispettare per far combaciare tra loro le componenti. Ma ormai io monto a memoria per esperienza».
Dopo il test degli impianti elettrici e la prova della convergenza, la vettura viene consegnata a un collaudatore e deve percorrere 50 chilometri su strada, in tangenziale fuori Modena, dove ci sono dei percorsi prestabiliti. Si chiama “test cliente”. Poi la macchina viene pulita e lucidata, pronta per essere venduta, perché la prova decisiva e finale è quella che riguarda la conformità estetica. Tutto il processo produttivo è gestito secondo il modello nipponico Kaizen. Nessun grande magazzino per lo stoccaggio dei materiali, solo alcune pile di cassoni posti appena fuori l’ingresso del padiglione.
La produzione è just in time: i materiali per costruire le supercar del tridente sono consegnati all’azienda giornalmente sulla base degli ordinativi, ciò evita sprechi e diminuisce i costi per l’azienda. L’unico passaggio che si svolge all’infuori dell’impianto principale è la verniciatura. Tornata ad essere un’esclusiva Maserati, l’azienda utilizza una vernice ecologica ad acqua. Questa fase può durare dalle due ore e mezza alle tre, in relazione ai due o tre passaggi di cui necessità il colore. I colori di base sono 7, mentre quelli fuori serie, che sono prodotti da carrozzieri esterni e quindi, se scelti, determinano un allungamento dei tempi di attesa, sono 27. La carrozzeria entra dunque in un tunnel con le pareti trasparenti dove dei bracci meccanici ruotano vorticosamente spruzzando il colore sulle lamiere. Ma nessuna autonomia di azione per questi arti: in Maserati non si fa uso di intelligenza artificiale, i programmi sono preimpostati e sono sempre avviati da un lavoratore che supervisiona al processo. «Da un punto di vista tecnico – afferma Lomio – l’automotive non potrebbe beneficiarne per ora, esistono ovviamente dei programmi automatici, ma la partecipazione umana serve sempre per farli partire».
Oltre al polo produttivo, punto forte di Maserati è lo showroom modenese, dove viene ripercorsa la storia del marchio e si getta uno sguardo al futuro. Infatti ad attrarre gli appassionati di auto sportive c’è, in particolare, l’esposizione di due pezzi unici completamente elettrici. La Gran Turismo Luce e la punta di diamante della velocità a trazione voltaica, la Maserati Folgore, che ha esordito nella scorsa edizione della Formula E (campionato dedicato alle monoposto elettriche). Presentata alla Milano Design Week dello scorso aprile, in occasione del 75esimo anniversario della GranTurismo, la supercar Luce, messa a punto dal programma “Fuori serie”, è prodotta in alluminio a vista (al posto della classica vernice) e, soprattutto, utilizza l’Econyl per gli interni. Derivato dalla rigenerazione delle reti da pesca abbandonate, questo tessuto in nylon riutilizzabile all’infinito è una delle fibre sintetiche più ecologiche in commercio. La monoposto Folgore, invece, tornerà a sfrecciare sui tracciati urbani della Formula E il prossimo 13 gennaio a Città del Messico.
Questo articolo è già stato pubblicato nel numero 14 di Quindici, il bisettimanale di InCronaca, in data 18 gennaio 2024.
Foto di Tommaso Corleoni.